Packaging a punch
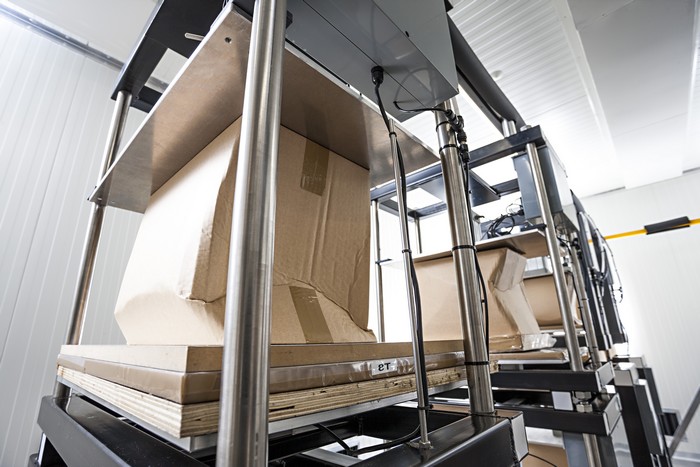
New Zealand packs a punch well above its weight in the packaging science space, with Scion hosting a unique and world-class set of capabilities and infrastructure for commercial testing, research and development.
It’s not a small coincidence that one of the world’s most advanced packaging research and testing facilities exists in New Zealand. With a $63 billion contribution to GDP in 2021, we are an exporting nation. Dairy, meat and fruit are among our largest export earners. Each of these food items exported needs to comply with a myriad of global food safety, sustainability and environmental standards.
With growing global demand and requirements for recyclable, reusable and compostable packaging, the eradication of singleuse plastics and significant challenges around food waste, supply chain logistics and differing market compliance around recyclability, being part of the wider conversation has never been more important for us as an export nation.
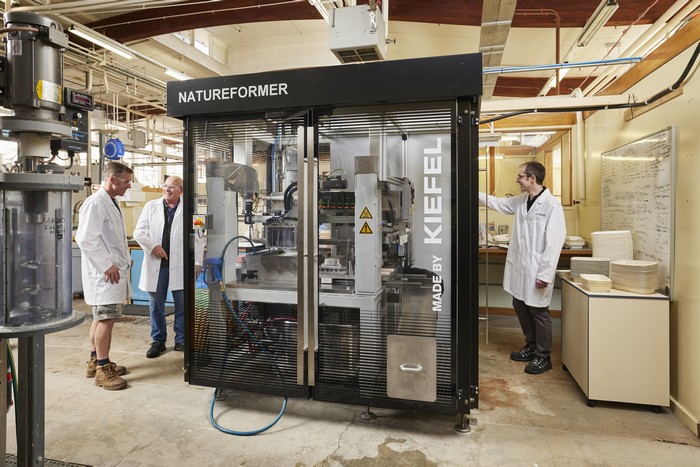
Scion invests $1 million in research and testing facilities
Scion is a global leader of fibre-based and plastic-based packaging research. As the packaging landscape rapidly changes, Scion has recently invested over $1 million in research and testing facilities, in order to ensure global packaging commitments can be met for New Zealand products.
Recently completed upgrades include doubling capacity for commercial testing of box performance in chilled supply chain conditions, called the WHITE Room (an acronym for weight, humidity, intervals (time), temperature experiments); doubling the capability of testing facilities for industrial disintegration to determine the compostability of packaging and products; and the purchase of a pilot-scale moulded fibre thermoformer machine to assist in the development of fibre-based packaging solutions.
Individually, these facilities are considered unique in the world, being among merely a handful of similar systems, but having all three on one independent site is, currently, the only one of its kind globally.
Of course, there is more to packaging than the above; digital packaging for traceability, food contact compliance and the development of bioplastics are also key research areas for Scion and assist in shaping the wider story of packaging in New Zealand.
Scion’s general manager of Forests to Biobased products Florian Graichen says for New Zealand, packaging is mission-critical. “For an export nation like us, packaging is absolutely vital. And it’s much more than just the material itself; what packaging enables is also significant.
“All our export markets are moving to reusable, recyclable or compostable packaging so it’s become much more than merely protecting the goods. Without sustainable packaging, you have severe risk to market access for all our brands and producers; hundreds of billions of dollars is underpinned by that.”
New Zealand also has its own aspirations around emissions mitigation, zero waste and creating a circular climate – none of that can be achieved without addressing packaging.
The wider context – packaging and food waste
In our ever-maturing awareness of how modern society impacts the environment, single-use plastics is controversial.
But there’s much more to the story: food waste.
According to the UN, as much as 30% of food produced worldwide is wasted. If global food waste was a country, it would be the third-largest emitter of greenhouse gas on earth. Big problem. Bigger than even plastic waste.
The conundrum facing many working in this space is that packaging plays a vital role in helping to reduce food waste and making sure products are in a fit-to-eat state by the time they reach the fridge.
Different markets also have different regulations around what constitutes sustainable food packaging, as well as different end-of-life infrastructure, meaning there is currently no one-size-fits-all solution.
So how do you create packaging that in and of itself is not an issue, while maintaining it’s still fit-for-purpose? If merely reducing packaging contributes to food waste, how can these two issues be similarly addressed?
This is the multi-billion-dollar question.
Work is already underway in many areas of the food production cycle here and overseas.
The Office of the Prime Minister’s Chief Science Advisor recently released a working report on combatting food waste, detailing what New Zealand is currently doing and what work is still needed.
The report, titled Food waste: A global and local problem, published in July 2022, highlights how the entire circular system needs to be taken into account – packaging design and manufacture, as well as end-of-life systems and end-market infrastructure.
Combatting food waste here and world-wide will require collaboration from many different stakeholders, including research, government and industry.
Scion’s role in the global conversation
So how does Scion fit into the global conversation?
Graichen says Scion brings together a unique number of elements to the packaging party.
“Where Scion packs a collaborative punch is with our decades-long experience in packaging research, science and innovations, our world-class facilities, and wide-reaching existing relationships both here and overseas.
“That means we can do true packaging research that is closely aligned with industry, which is absolutely unique.
“We are able to do the actual science behind packaging – including materials and performance – and then link it back into industry through the hundreds of small to large companies we work with. That capability doesn’t exist anywhere else.”
He says Scion’s knowledge has come full circle in terms of its historical work in the pulp and paper space.
“The need for fibre-based packaging is increasing rapidly. We can use the work done in the past and re-package it to make it relevant for the future, particularly as we already have the recycling options for paper-based products.
“The two opposing factors of single-use plastics and food waste will require significant ingenuity to combat – at policy level, science level and company level. Scion has those relationships already on which to draw from.”
Scion packaging research leader Kate Parker says increasing capacity for commercial testing and in-house research and development is critical for supporting New Zealand’s primary industries.
“There is a huge global push to make packaging recyclable, reusable or compostable, with many countries introducing legislation and targets around what they are and are not willing to import.”
Scion’s capability also enables New Zealand to be part of the conversation around creating international standards.
“Part of upgrading our facilities enables us to create good tests for fibre recyclability, because there are currently no universally accepted standards; they’re all focused on plastics. Currently, countries have their own set of standards, which means every market is different.
“New Zealand needs the capability to be able to test to those standards here, as well as support our primary industries to be able to meet market requirements and recycle more fibre onshore,” says Parker.
For New Zealand, our largest export markets are Europe, China, the US and Australia – all of which currently have different regulations around packaging and recyclability.
Parker says part of the work Scion does is not only about giving New Zealand industry options, but also helping them understand differing compliance.
Fibre-based R&D
Scion’s recent investment in facilities has allowed it to research new bio resources for packaging and waste.
“As we look at working with new bio resources to create packaging, it’s also a way of engaging with producers of agrifibre waste across New Zealand and supporting more recycling of fibre,” Parker says.
“We still have big waste streams in New Zealand because we don’t have the products to turn it into. Using what’s considered waste residue and turning it into new material resources that can be used is a big part of what we do.
“With the global push for more fibre packaging, many companies are looking at what options are available. Our role is to support New Zealand industry to move into that new space.
“Our upgraded facilities also mean we can take into account the bigger circular bioeconomy picture. We’re able to consider the full life cycle analysis of current and emerging new materials – feedstock, water, energy, transport – plus performance and what happens at end-of-life.”
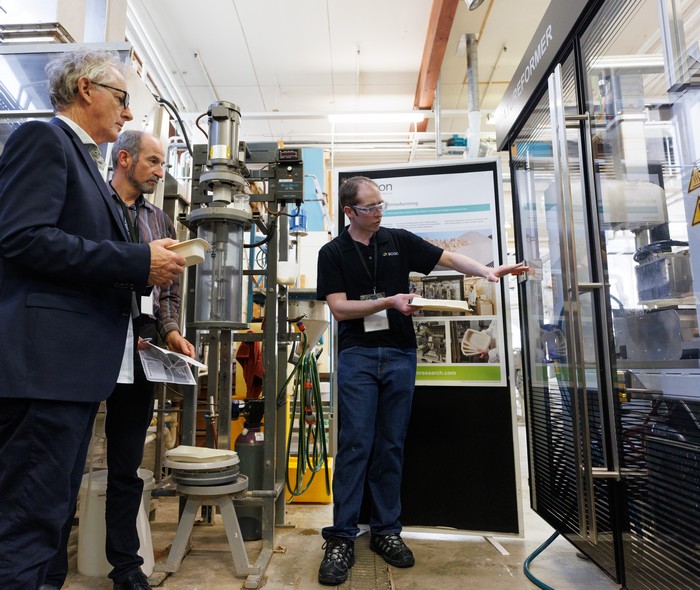
Forming a new path – the new Thermoformer
Scion’s Kiefel moulded fibre thermoformer arrived in June 2022. Paper and cardboard – dissolved in a water bath – create the raw material, known as pulp. Through application of pressure most of the water is removed and the wet basic form is created. In the next step, the remaining moisture is removed and the basic form is dried by applying high pressure and temperature. The combination of the applied heat and pressure results in a very robust material for packaging.
The pilot scale industrial machine enables different pulps to be trialled rapidly for packaging with relatively small volumes of material needed, 1-2kg of dry pulp being sufficient.
Scion has trialled different pulps in the thermoformer, with the ability to collect data such as how much energy and water is used to create trays from each different pulp, as well as the percentages of recycled fibres that can be used in pulp before structure and performance is affected.
In the short term, the goal is to support industry to make the transition into new alternative packaging.
Long term, Scion sees its role in this space as researching different materials and fibre blends for those alternative packaging products, improving performance through lightweighting and mould design, as well as being able to offer an alternative use for recycled fibre waste in New Zealand.
Non-standard fibre streams, for example, which would not be available in sufficient volumes for papermaking, such as hemp hurd or agricultural residues, could be a valuable resource in this context.
Box it up baby
Validating new technology and materials is a crucial part of R&D and that’s enabled by the WHITE Room, which simulates supply chain conditions such as temperature, humidity and weight.
Imagine apples, kiwifruit or dairy products being exported to northern hemisphere markets. These food items are packed in boxes for weeks, need to cross the equator and withstand being crushed by boxes stacked on top of them.
Scientist Dr Kelly Wade says the WHITE Room gives the packaging team the ability to create a model, then make packaging based on that model and test it in real-world conditions to understand performance.
“Traditionally, boxes are specified based on their shortterm crush strength and safety factors to ensure they don’t fail, which can lead to over or under-specification.
“Now, with supply chains so stretched the world over, it’s become more important to minimise weight, size and transport costs, while still maintaining performance. Better understanding of long-term box performance offers the potential to optimise box specifications.”
Wade says ultimately, the goal would be to re-design the cardboard box with the knowledge gained and continue to test within industry to make sure it’s viable.
“Box performance is no simple thing. Paper composition and how it is converted into board, how the box is cut, glued and taped, printing technique and handle placement can all affect performance of the box itself. Other factors such as filling of the box, stacking arrangement and environmental factors like temperature and humidity can further influence the response of the box.
“And they’re all on the table as things we can test using the WHITE Room. Ultimately over time, all boxes eventually fail. We want to understand the science behind that.”
The WHITE Room is also used for commercial trials by companies wanting to further optimise their own systems and packaging. Despite capacity doubling with the recent upgrade, it is still booked up with clients for months in advance.
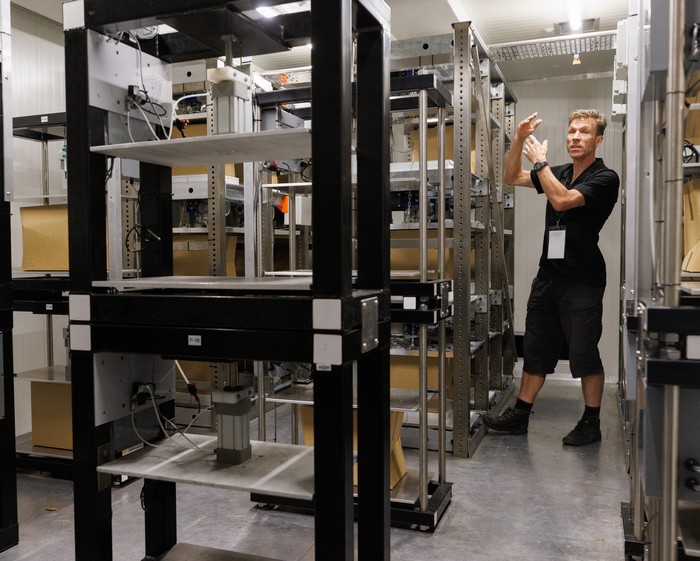
Compost your cappuccino
As new packaging and materials are developed, it is essential they live up to their compostability claims. Do they in fact disintegrate? And what happens to the compost once materials have broken down?
Scion’s newly upgraded biodegradation facility allows compostable and fibre-based packaging to be tried, tested and certified, as well as provide knowledge and information about the wider impact of biodegradable packaging on the environment.
“In terms of compostability, we aim to support the transition of materials to being compostable,” says Parker.
“It’s becoming more important that packaging materials are actually certified compostable and it’s important for New Zealand industry to be able to have access to that type of testing facility. The closest other facility of its kind is in Thailand.
“We work with the Ministry for the Environment, for example, to support them in moving New Zealand towards a new circular bioeconomy, and the phase out of single-use plastics.”
Parker says as well as industrial disintegration tests, which take around three months, the facility enables both Scion and commercial clients to undertake biodegradation tests (measuring the conversion of carbon in the original material to carbon dioxide) and ecotox testing (where the resulting compost generated during original material breakdown is still viable in terms of seedling growth and worm health).
Wrapping up
In a [sustainably packaged] nutshell, Scion is committed to working towards how New Zealand can do things better and smarter.
Bringing together industry, infrastructure, R&D and legislation, as well as ensuring dissemination of information and ongoing collaboration, is the only way to combat the challenges we find ourselves wrapped in.
Talk to our packaging team to find out how Scion’s research can support your organisation’s sustainability goals. For more information, please contact Alec Foster.