Biomaterials in action: Pearl farming in the Pacific
A promising aquaculture biomaterial trial is currently under way in Tahiti to help the pearl farming industry in French Polynesia become more sustainable.
French Polynesia is well known for its crystalline waters and sunny tourism.
But being a small, remote island nation made up of more than 100 islands spread over an area nearly the size of Europe, with a population of 280,000 people, brings a unique set of challenges – particularly when it comes to resources and waste.
Pearl farming is the second largest economic earner in French Polynesia behind tourism and a major source of employment in remote islands. However, it is also known to significantly impact the environment through plastics pollution.
A lot of work has been going on in recent years to promote more sustainable aquaculture practices and improve thinking about how to use and discard materials with greater circularity.
With aquaculture an important industry, plastic and what to do with it has been a substantial chunk of the issue.
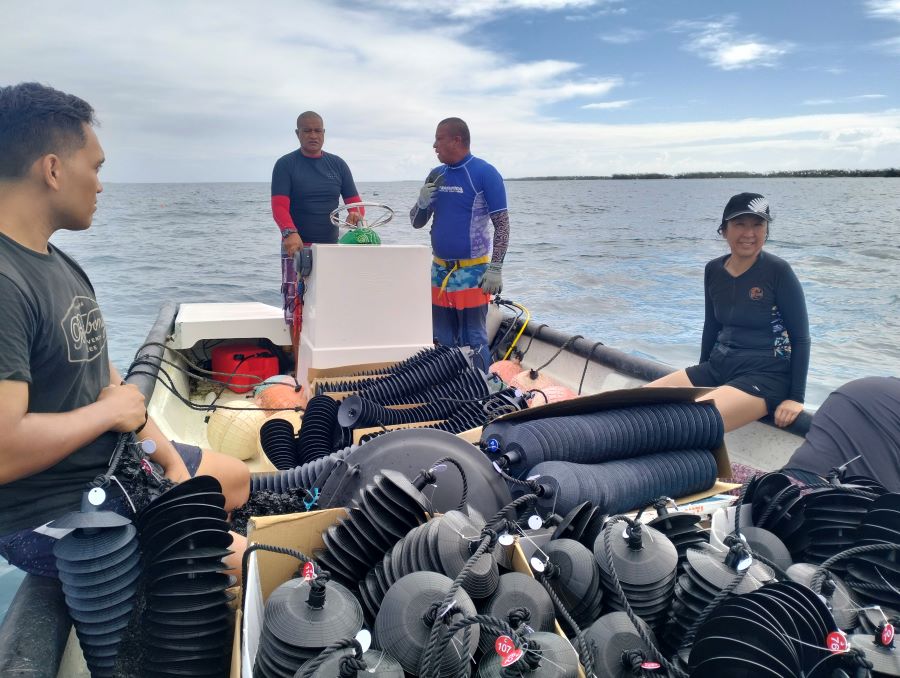
The challenge
The current materials used for oyster collectors – vertical lines of plastic shade-mesh, similar to tinsel, which oyster spat attach to and grow – are notorious for disintegrating and leaving microplastics in the picturesque lagoons.
It’s also not really known what to do with plastic waste once it reaches end-of-life and some ends up being burnt or buried. Professor Nabila Gaertner-Mazouni and her team from the University of French Polynesia (UPF) first approached Scion in 2016 for help with the mounting plastics issue, but it wasn’t until 2020 that funding was received from the French Polynesian government and an agreement was signed around how to create a more sustainable aquaculture industry.
UPF project team member and doctor in marine ecology Margaux Crusot says UPF approached Scion initially because of its expertise in biomaterials and development of sustainable solutions.
“At UPF, we provide the biology and ecology expertise necessary for developing the solution, while Scion, with their knowledge and expertise, can translate our needs into concrete solutions.
“We have been very pleased with this collaboration and complement each other well in our understanding of things.”
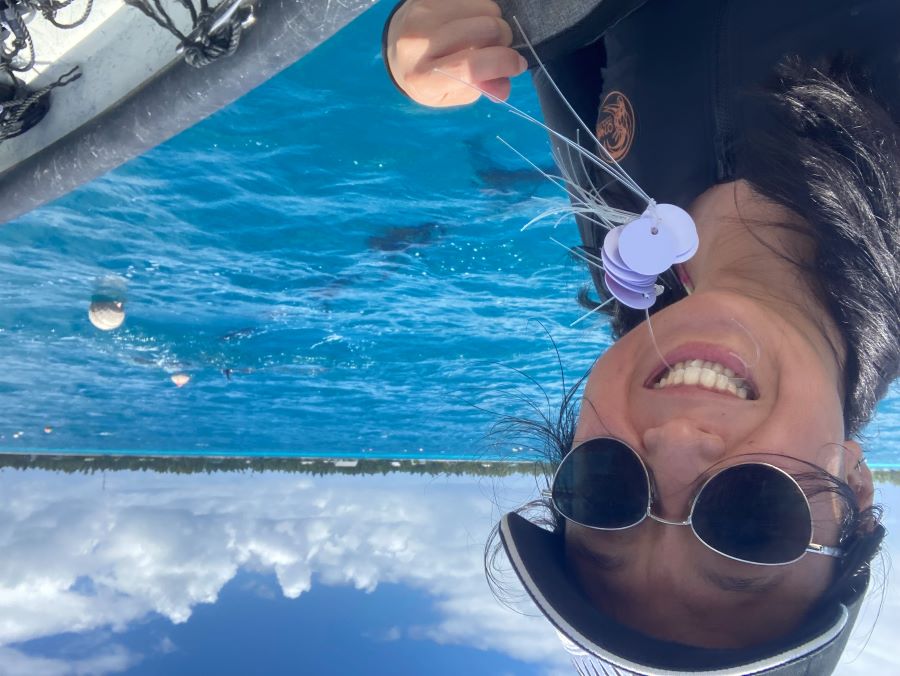
The beginning of a solution
In her previous role as Scion research group leader for Materials, Engineering and Manufacturing, Marie-Joo Le Guen and her team began looking at alternative materials for the traditional oyster collectors.
After UPF assessed a number of options for alternative collector shapes, they decided on a coupelle – a slightly concave disc with a hole in the middle. Used elsewhere in the edible oyster aquaculture industry, but not for pearl oysters, there wasn’t an existing bio-based product available in the coupelle shape.
Materials technologist Maxime Barbier set about developing a formulation based on existing research and a specific set of requirements from UPF, in addition to being suitable for 3D printing.
The final biomaterial, named Black Pearl, was developed and compounded in Scion’s extrusion lab in 2020. After initial lab trials to prove feasibility, material was sent to Scion’s commercial partner Imagin Plastics in Auckland and made into 3D printing filament.
Initial trial
With an initial small-scale deployment planned by UPF in Tahiti, 2400 coupelle prototypes were needed. To 3D print such a large number, Scion’s FDM 3D printers were increased to a fleet of eight, thanks to UPF funding, and affectionately referred to as the Avengers.
All eight Avengers had to be re-coded for a new method of printing. Known as non-planar printing, the process significantly decreased the time taken to print each coupelle and saw parts printed freeform, instead of as individual horizontal layers in sequence, allowing for less material being used.
The trial, which took place in 2020, proved the coupelle shape was good, providing protection and shade for the spat to settle into.
Existing HDPE (petroleum based high-density polyethylene) coupelles and shade-mesh collectors were also tested alongside the bio-based coupelles and it was found the amount of settlement was greater on the bio-based material, meaning they attracted more spat.
Le Guen says the predominant invasive species appeared not to like the biomaterial as much as the HDPE, which was a double win.
The trial revealed the 3D printing method was not sufficiently resistant, with some coupelles breaking up prematurely due to insufficient layer adhesion – another valuable piece of the puzzle. It still provided enough data to understand the material and shape both had promise.
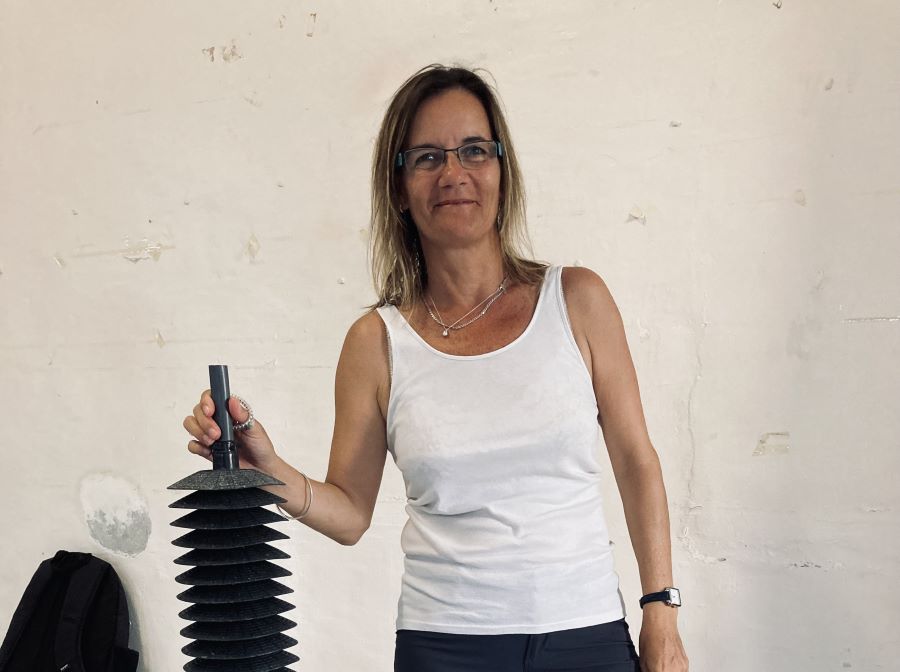
Scaling up
From there, a new trial was established using an alternative production method. Scion produced 750kg of compound in New Zealand, which was then shipped to Tahiti, where local company, Plastiserd, injection moulded the new coupelles.
Plastiserd produced 12,400 coupelles for UPF to deploy across three different locations, taking into account the vastly different conditions seen throughout French Polynesia due to being spread over such an extremely large area.
Scion’s team lead for the Additive Manufacturing and Emerging Technology team, Rob Whitton, along with Le Guen and Barbier, travelled to Takapoto Atoll in Tahiti, in October 2023 to help with the first deployment of the upscaled trial.
As with previous trials, three types of collectors have been included – the plastic HDPE coupelles, the new bio-based coupelles and the traditional plastic shade-mesh – alternating along a 200m line. Each collector is 1.2m long, sitting 6m below the surface of the water, which is around 25 – 50m deep.
The trial will run for two years, monitoring the compatibility of the new collectors compared to the old ones, with collectors monitored every six months.
A second trial looking at the biodegradability of the biomaterial is running alongside this.
Scion’s visit also included community engagement, with both the university and Scion hosting local pearl farmers and fishermen, and the general community, to help educate them around the need for change.
Whitton says getting the community on board will be a big factor in success.
“We were able to see what UPF are trying to do in terms of being able to convince the local aquaculture industry this is a good move. People are quite skeptical, particularly of scientific institutes coming in with new options.”
Strength of collaboration and connection
As with many things, collaboration and connection is key, particularly in isolated communities. While in Tahiti, UPF organised a biomaterials conference where Scion presented its experience and capabilities.
The Scion team also spent time meeting with the Tahiti industry working with biomaterials and natural fibres.
“We built some valuable links with the local biomaterial industry,” Whitton says.
“They’re a small economy so they’re quite limited with what they can do, but they have some interesting feedstocks they’re working with – like banana leaves and coconut fibres. They’re being used for the likes of aquaculture ropes and moulded-fibre packaging.”
Hosted by UPF, Scion also visited other local industrial companies, including Pacific Biotech, a fermentation company working with EPSs (exopolysaccharides) and PHAs (polyhydroxyalkanoates) – or in layman's terms, biopolymers produced from bacteria that can be used for making the likes of bioplastics and biofilms.
Scion and Pacific Biotech have since entered into a material transfer agreement, meaning the company will send material to Scion’s labs for testing, leading to future collaboration.
What’s next
Scion’s relationship with UPF has continued to consolidate and Le Guen hopes this is not the end of the journey.
“If this trial is successful for a specific species, that’s very exciting for us.”
Crusot says it has been a pleasure working with Scion.
“The team is very easy to work with, and it has been a pleasure collaborating both at Scion and in French Polynesia. Additionally, our results clearly demonstrate the success of the collaboration, and I would be delighted to continue working with them.”
She says developing a biodegradable alternative collector has many associated benefits for French Polynesia, such as substantially reducing waste, establishing groundwork for the development of a local production industry with less reliance from overseas and creation of local jobs, promoting technical innovation and providing strong visibility for French Polynesia, which would be the first, based on current knowledge, to provide a biodegradable bivalve larvae collector globally.
As with all change, it won’t be overnight, but things are looking pearly.