These boots were tanned with pine bark
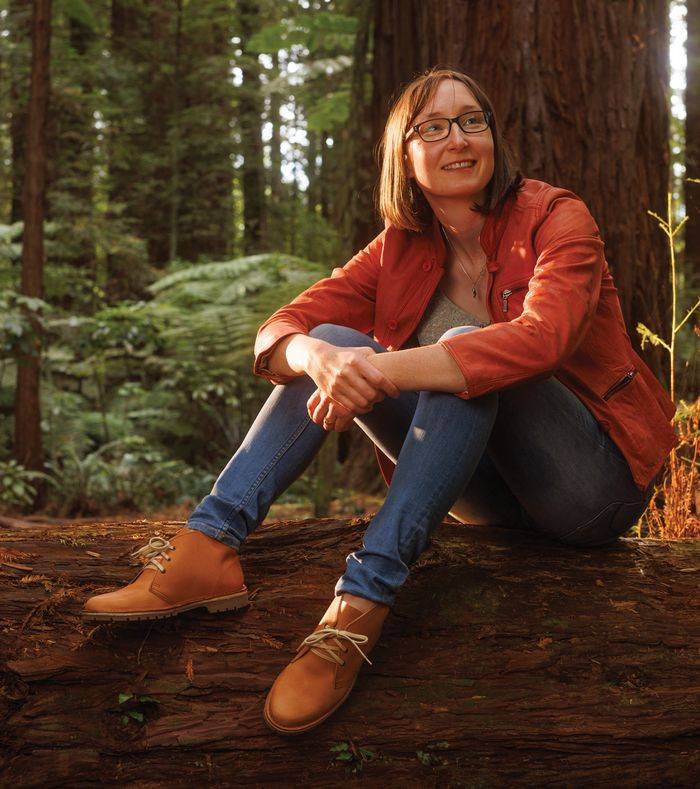
“Has the New Zealand leather industry been barking up the wrong tree?” quips Geoff Holmes, director of the Leather and Shoe Research Association of New Zealand (LASRA).
Holmes and other industry representatives started talking to Scion two years ago about developing a local replacement for imported tanning agents. Holmes says the use of vegetable tannins to tan leather dates back centuries.
“They produce leathers of rich texture and a fine patina which only develops further over time and are used in luxury leather goods made by brands such as Louis Vuitton, Hermès and Burberry."
Scion did not have to look far to find a local source. The New Zealand pine industry produces two million tonnes of pine bark a year, most of which goes to waste. When radiata pine trees are felled for export, the bark has to be removed for biosecurity reasons prior to export, and the bark is discarded, with just a fraction used for low-value applications such as garden mulch.
In 2018, Scion won an $11.4 million Endeavour grant across five years from the Ministry of Business, Innovation and Employment (MBIE) to pioneer the feasibility of a bark biorefinery that would extract tannins and potentially create a range of valuable chemicals, nutraceuticals, cosmeceuticals, pharmaceutical intermediates, and green adhesives for building products.
New Zealand currently imports all its tanning reagents based on plant tannins or heavy metals (chromium). The latter account for 85-90 percent of tanning agents used. There is a growing demand for plant tannins globally and the COVID-19 pandemic has shown us there are many advantages to having local and sustainable supply chains. Using pine bark tannins will reduce New Zealand's carbon footprint and transport costs by reducing imports (usually by ship) of tannins. Furthermore, it will utilise a plentiful local resource, otherwise wasted, create a range of new jobs, and will free industry from worries about disrupted supply lines.
Scion High Value Biorefineries portfolio leader Dr Stefan Hill says this research has represented a combination of government and private research institutes working with industry.
“It demonstrates New Zealand products that reduce our dependence on imports and provides new exciting opportunities, building towards a sustainable circular bioeconomy.”
The boots pictured – the first pair to be made with leather tanned using Scion’s New Zealand pine bark tannin – are the first proof of concept. They were handcrafted in late 2021 by McKinlays Footwear in Dunedin – New Zealand's only remaining domestic shoe manufacturer of any scale, according to LASRA.
Graeme McKinlay, the owner of McKinlay’s Footwear, says, “The bark-tanned leather cuts and handles in the factory as well as any chrome tannage, and we look forward to seeing more in the future.”
Holmes adds, "Their distinctive natural colour may appeal to leather fashionistas and open a new niche market for the New Zealand leather industry."
Most of New Zealand’s 2.4 million animal hides (a by-product of the beef industry) are exported for others to finish and craft into high-value products. The only remaining finished leather tannery in New Zealand is Tasman Tanning in Whanganui, which employs 250 people to finish 7,000 hides a week. The material used for the trial run was sourced from the company part-processed, ready for tanning with Scion pine bark tannins.
There is still a way to go with the Scion feasibility study. Organic chemist Dr Hilary Corkran is perfecting the extraction process, and the team, led by Dr Marie Joo Le Guen, is fine-tuning the economics of a biorefinery with industry. It would compete with other tannin sources, particularly wattle tannins from South America and Africa. The fact that the tannins are produced locally and sustainably, and are part of a complete New Zealand story, adds value.
Economic factors include the siting of one or more refineries to minimise bark collection and transport costs. After chemicals are extracted from the bark, the 85 percent mass leftover can be compressed into fuel briquettes as a coal replacement or used as specialty medium in horticulture.

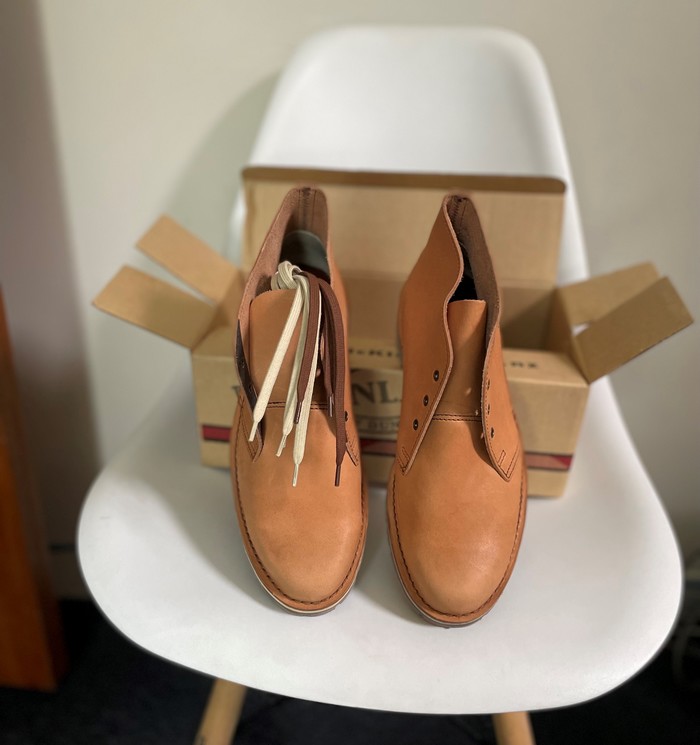
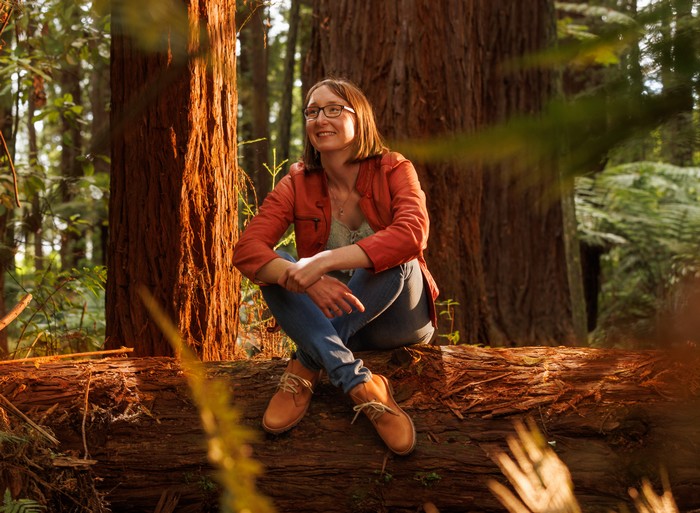